Innovation Story: Proterra® Uses KYDEX® Thermoplastics in All Electric Buses
Proterra® was founded in 2004 by entrepreneur Dale Hill. He believed Proterra could lead the industry by combining innovations in high-performance electric propulsion with lightweight interior and exterior design. Hill assembled a team of engineers that began working to revolutionize mass transit by creating a new alternative: a 100% battery-electric bus.
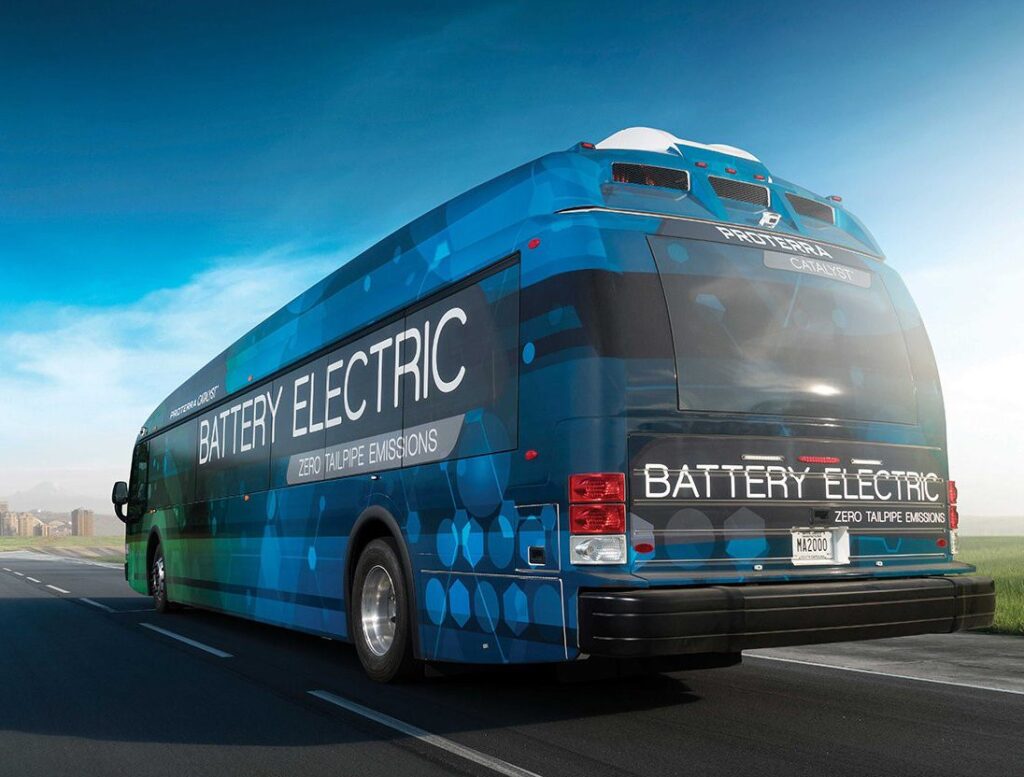
The Challenges
Proterra’s goal was to design an all-electric drivetrain powerful enough to move a fully occupied bus through city traffic. In addition, the battery had to have enough energy storage capacity to be able to travel significant distances between battery recharges. The bus had to be both cost-effective and efficient, with competitive pricing and low operating costs.
Beyond the engine, design materials needed to be lightweight for greater efficiency and range; attractive, for passenger appeal; and durable, to reduce replacement costs. Further, materials would have to meet transportation industry safety standards and be produced in a way that worked with Proterra’s supply chain requirements.
The Solution
Proterra’s all-electric buses use KYDEX® 6200, KYDEX® T, and ALLEN® 5160WHG for internal and external applications. These lightweight materials significantly reduce weight versus more traditional materials, such as fiber-reinforced resins or metal, thereby increasing vehicle efficiency and range. At the same time, these materials provided a range of texture and colour options that were refined to maximize colour stability under UV exposure. The materials are also recyclable and therefore contribute to a better, more sustainable environment. In addition, all materials meet Motor Vehicle Safety Standards, and KYDEX® 6200 is compliant with Docket 90, a set of test procedures intended to assess not only flammability but also smoke emission characteristics. SEKISUI KYDEX’s rapid order fulfillment helps Proterra keep its supply chain running smoothly.
SEKISUI KYDEX’s relationship with Proterra is defined by collaboration and technical support. Using designLab®, Proterra leveraged KYDEX’s mass transit experience and thermoformer relationships to make highly-informed decisions about material, colour, and finish.
Results
SEKISUI KYDEX’s lightweight materials help Proterra` vehicles work more efficiently, producing zero tailpipe emissions, versus the 229,167 pounds of CO2 emissions produced annually by a standard diesel bus. Using SEKISUI KYDEX’s high-quality, lightweight, recyclable materials, Proterra has created the best zero-emission alternative to traditional steel buses.
This article was originally published by SEKISUI KYDEX, LLC.