Here at ELeather, we believe that too many of world’s limited resources are being unnecessarily wasted. By using a natural product that would otherwise be sent to landfill, we are evolving leather to become a more responsible, desirable and performance driven material – engineered leather.
Engineered for Superior Performance
In short, engineered leather is an advanced material made with up to 50% traditional leather fibres. It retains the luxurious look and feel of traditional leather at the same time providing enhanced comfort associated with soft trimmings. It’s engineered for performance meaning it is scuff and scratch resistant and due to controlled stretch it maintains its form and shape with no bagging, even after prolonged period of use. This translates into longer lifetime and reduced need for replacements.
Our patented production process ensures consistent colour and gloss throughout the life of a product. Thanks to improved hygiene the product is low maintenance and presents a cost-effective solution, especially for high impact public spaces and transport operators.
Engineered leather is a stable, predictable material which makes patterning and cutting more efficient with higher yield per roll and less waste as a result.
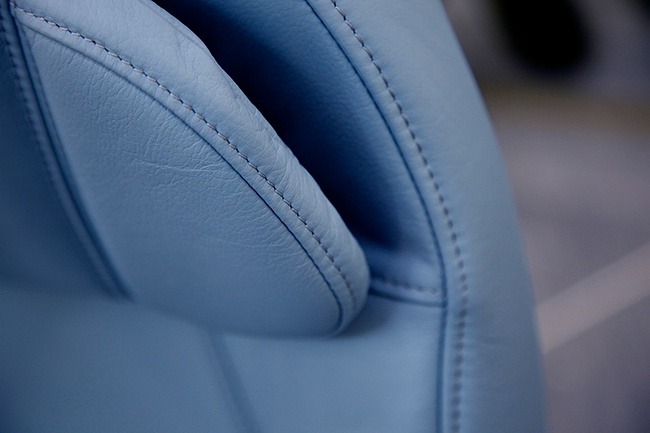
The Pioneer of Engineered Leather
Our engineered leather has been in production for 13 years and over the years ELeather has grown and expanded to supply transport, footwear, lifestyle and public spaces markets. As a global business, we have a team of dedicated and experienced industry experts located worldwide that enable us to function as a customer centric organisation. The quality, passion and integrity of our people and the relationships we build are key to our future.
We are proud to supply over 200 airlines, including four of the world’s largest, as well as transforming more than 12,000 rail vehicles. World leading brands such as Nike and aviation giants such as Aeromexico have trusted ELeather with great results.
Our product is certified across major manufacturing regulations and we’re proud to hold ISO9001, ISO14004 and BS OHSAS18001 certifications to showcase high standards to which we hold ourselves.
Driving Material Change
Taking more care of the world’s most previous resources builds better reputations. Fact. We have saved thousands of tons of leather from going to landfill, instead using it to create material of choice for many global brands across multiple industries.
The production process of engineered leather not only uses 90% less water (compared to full grain leather) but 95% of water used is then recycled and used again. Fibre bonding is achieved using only water and without the need for adhesives that can be harmful to the environment. Going one step further, ELeather’s wet production waste is converted into fertiliser used by local farmers while dry waste is recycled locally to further reduce our carbon footprint.
How It’s Made
Taking our most precious commodity – water – we have developed and patented a manufacturing process that uses hydroentanglement technology to lock traditional leather fibres within a high-performance core.
- Shavings, trimmings and split hides are diverted from landfill and then ground and filtered to produce individual leather fibres.
- A strong textile core is laid between two webbed rolls of leather fibre, which are interlinked during the process of hydroentanglement. This negates the need for adhesives and the result is a structure similar to the one of traditional leather.
- The substrate material is finished with the customer’s choice of colour and texture.
The result is engineered leather – a high performance material with all the benefits of traditional leather but supplied on a roll without natural markings or defects.
Higher Yield for Cut and Sew
Engineered leather is more evolved than traditional leather and it’s got its own unique properties which make it behave different to its traditional, synthetic or textile alternatives. Thanks to a controlled stretch in one direction it retains its shape better when in use.
The material is produced on a roll with even colour and gloss throughout meaning a higher yield and less waste. There is no need for high sewing machine foot pressure as the thickness and texture of the material is uniform although use of good quality tools is recommended. Conventional joining techniques can be used without issue and thanks to its strength, engineered leather can be trimmed within 2mm of stitch seams.
Easy to Look After
Due to built in functionality, engineered leather is easy to clean eliminating frequent chemical cleaning requirements. Regular light cleaning using soft brush or vacuum to remove loose debris is recommended. This can be followed by wipe down with a light moist cloth.
We test our product performance to the properties specified in the ELeather Product Specifications. These specifications have been derived with the assistance of recognised independent Specialist Trade Associations, and Consultants in the Industry. Thanks to our zero compromise on quality with 100% performance approach, we are able to provide brands with competitive advantage.
Request a sample and join the evolution.