Whether you’re operating a fleet or running a smaller workshop, there’s one thing that’s never going to change about vehicles: they’re going to need testing. And lots of it.
Investing in dedicated equipment can seem like a big expense at first. But when you start looking at the long term – and the savings you could be making – most bits of kit start paying for themselves after the first year or two.
So how exactly can testing equipment save you money? Let’s get into it.
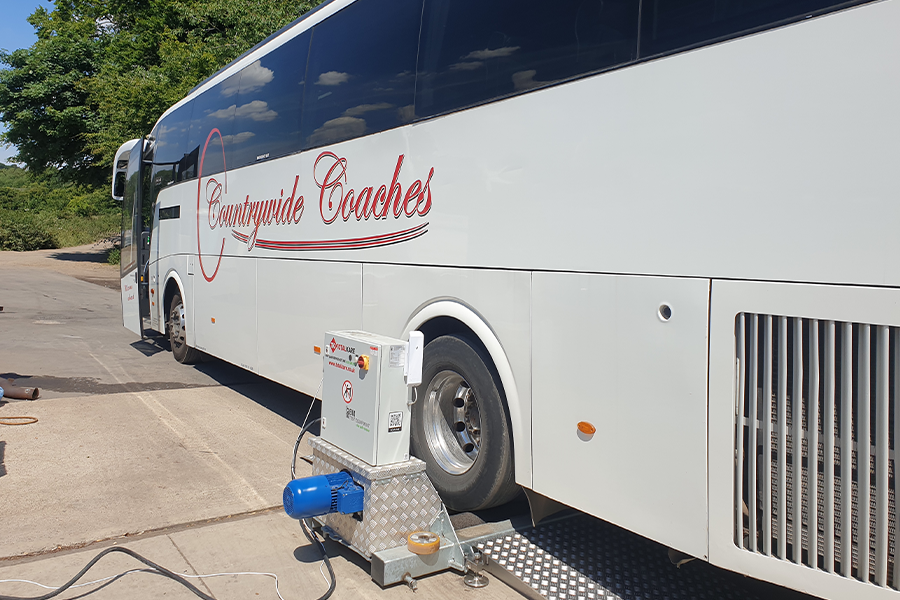
You Pay Your Own Rates
When you outsource your vehicle testing, you’re not just paying for the test itself, you’re paying for another company’s costs – their wages, their rent, their maintenance, and their utilities.
All of those costs are outside of your control. If the company doing your tests is getting a bad deal, that means you’re getting a bad deal. If they’re not cost-effective, then you’re not cost-effective – and you could be overpaying without even realising it.
But with your own testing equipment and your own teams behind it, you know exactly what you’re spending money on (and exactly how efficient it is).
You’re paying the wages and bills that you’ve chosen carefully for your own business – at the level that works for your budget, your cash flow, and your own sense of value.
You’re not at the mercy of some other company’s idea of efficiency. And that means you’re free to make your own savings on the cost of the tests.
You’re Getting More Value from What You Have
You might have salaried workers who don’t fill up their time – or you might even have a workshop with some unused space.
If that’s the case, you’re effectively paying twice for every test you outsource – either for the rent on unused ground space, or the salaries of the workers who don’t have a full schedule.
But when you bring your vehicle testing in-house with dedicated equipment, you’re putting your own teams and premises behind it. You’re letting nothing go to waste, and you’re saving money along the way.
For workshops with a lot of free space, that could mean adding a new testing lane with an In-Ground Brake Tester – cutting your costs on outsourced tests, and squeezing the full value out of your workshop floor.
For workshops with less free space, that could mean a compact and mobile Diesel Smoke Meter – so you can start your own in-house emissions testing, and reduce your reliance on outside businesses.
Instead of lining the pockets of another company, you could be investing in your company and your teams – by bringing more jobs on-site, and getting the most out of the premises and workforce you’re already paying for.
You’re Skipping the Fuel Costs
When you ship out your testing jobs to an outside company, you’re already wasting money and time.
Every vehicle test means a round trip to the test centre. You’re pulling a driver away from other bits of work, and you’re adding to the costs of wear and tear by putting a vehicle out on the road.
And of course, you’re burning up fuel on a trip with a heavy vehicle. That’s not just an unnecessary cost – it’s an unnecessary addition to the harmful emissions you’re causing.
But with your own in-house testing equipment, you’ll be sharing a roof with the test centre. And that could mean saving hundreds of miles per year.
You’ll Reduce Your Downtime
Some workshops might already have a few pieces of testing equipment installed on their premises.
That’s a great start, and you’re already saving money. But if you’re not making the most of the time spent in the bay, you’re still losing out. And if you’re still travelling to test centres to fill in the gaps, you’re still wasting money and time.
So if you’ve already got a vehicle that’s in position and getting tested, why not give it the full works while it’s there?
With the right combination of in-house testing gear – like our compact Headlamp Testers, our mobile Wheel Alignment System, and our Mobile Brake Tester – you can build a comprehensive testing station that does multiple things at once.
You’ll get through more tests in less time, without any need to move or reposition your vehicle. You’ll be reducing your downtime, and spending more time with your vehicles out on the road and earning.
You Only Pay Once
Lots of companies are happy sending their fleets off to third-party test centres – until they start to fail.
When a vehicle fails a test, you’ll need to bring it back to base and make repairs and improvements. You’ll then need to ship it off again for a retest – paying a whole new fee to the test centre, as well as paying for more fuel.
It’s not an efficient way to go. And it could easily be avoided by bringing your testing in-house.
If you fail a test in your own premises, you can be ready for a second test in hours. You can make the adjustments and repairs your vehicle needs, and start over straight away. In some cases, you won’t even need to move the vehicle between the two tests.
And the best part?
You won’t be paying an extra fee to book a second test. It’s all right there and ready, and no one’s going to charge you.
Ready to Take Control of Your Testing?
Buying your own equipment isn’t a modest investment. But in the long run, it could be one of the best financial decisions you make.
So if you’re looking to ditch the test centres and bring the equipment in-house, check out our full range of testing equipment in our online shop – from brake testers and shaker plates to emissions and wheel alignment.
This article was originally published by Totalkare Ltd.